
AI-Powered Education for Enhanced Performance in Electronic Manufacturing
A leading electronic manufacturing company faced persistent challenges with product traceability and the limitations of legacy systems. Recognizing the potential of artificial intelligence (AI) to address these issues, the company initiated a comprehensive employee education program focused on AI best practices.
This case study examines the thought processes, methodologies, and outcomes of this initiative, demonstrating the transformative impact of AI education on employee performance and operational efficiency.
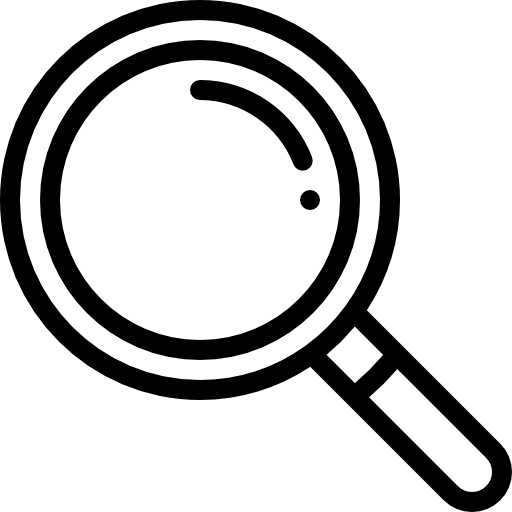
OBSERVATION AND ANALYSIS
The company conducted a thorough assessment of existing manufacturing processes, identifying bottlenecks in product traceability and limitations within outdated systems.
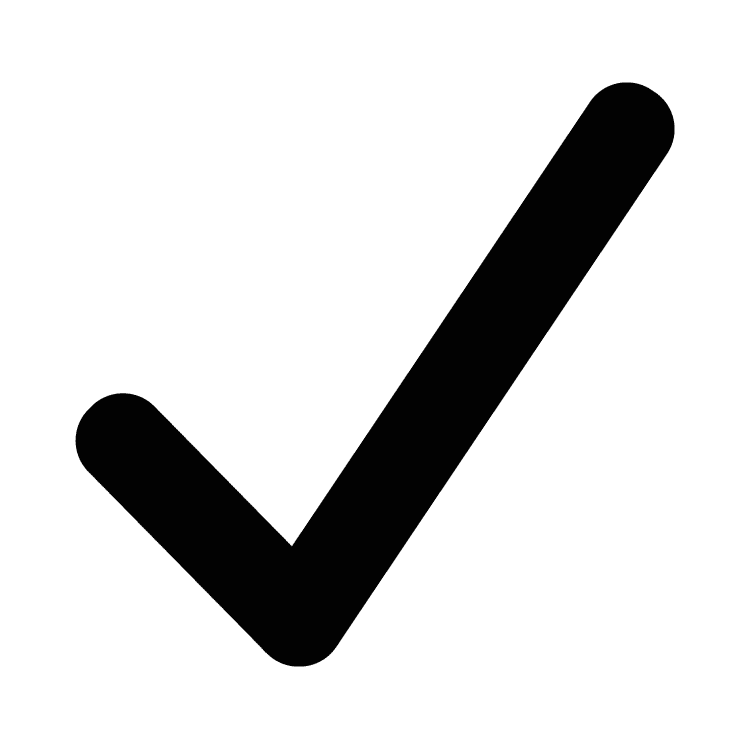
PROBLEM STATEMENT
The core problem was defined as a lack of effective AI education and training, hindering employees' ability to leverage AI for improved product traceability and system optimization.
Problem Identification
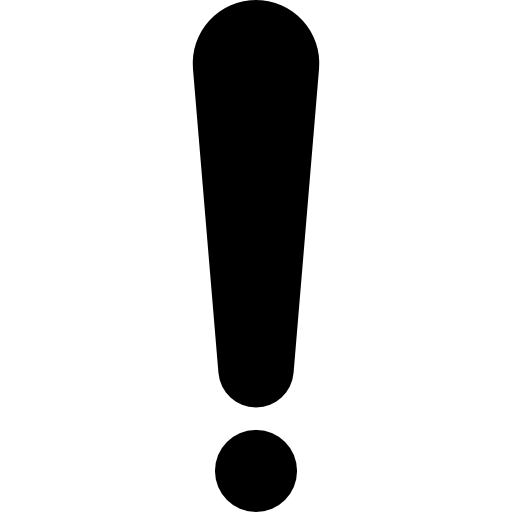
HYPOTHESIS FORMATION
It was hypothesized that traditional training methods were insufficient for equipping employees with the AI knowledge needed to overcome these challenges.
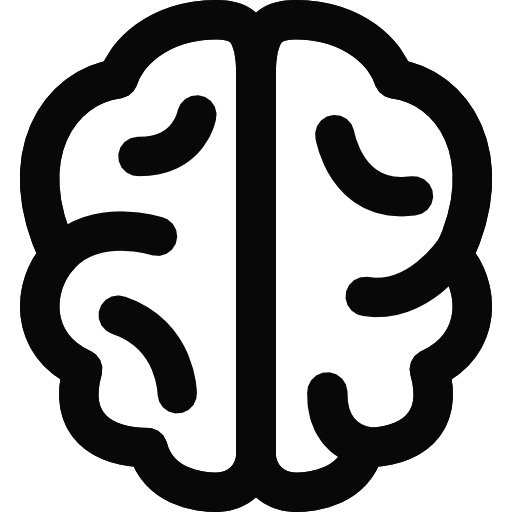
BRAINSTORMING
A variety of potential educational approaches were explored, including online courses, workshops, mentorship programs, and simulations.
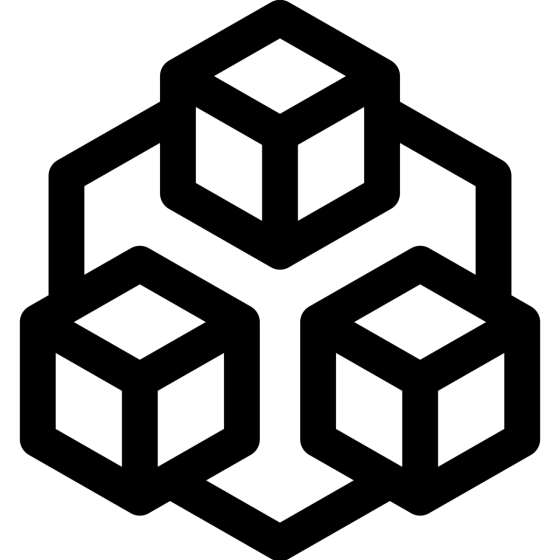
CONCEPTUAL FRAMEWORK
A blended learning framework was developed, combining theoretical instruction with practical, hands-on application of AI tools and techniques within the manufacturing context.exclamation
Solution Conceptualization
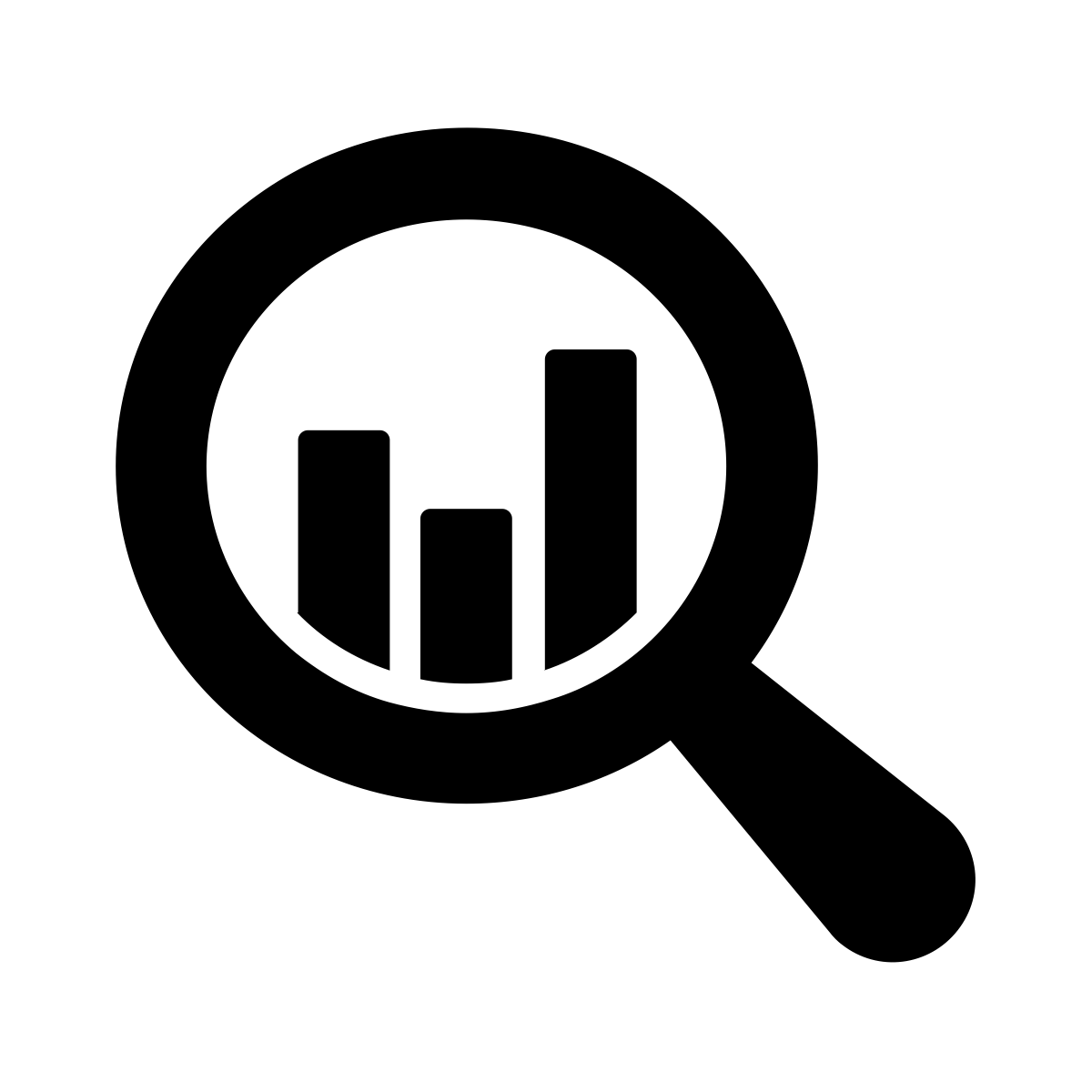
FEASIBILITY ANALYSIS
The feasibility of each approach was evaluated based on technological resources, budget constraints, and the company's learning culture.
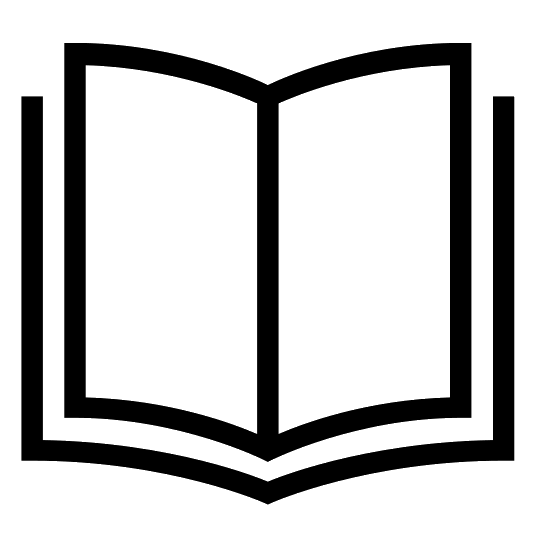
LITERATURE REVIEW
A comprehensive review of existing research on AI education and its application in manufacturing was conducted to identify best practices and potential pitfalls.
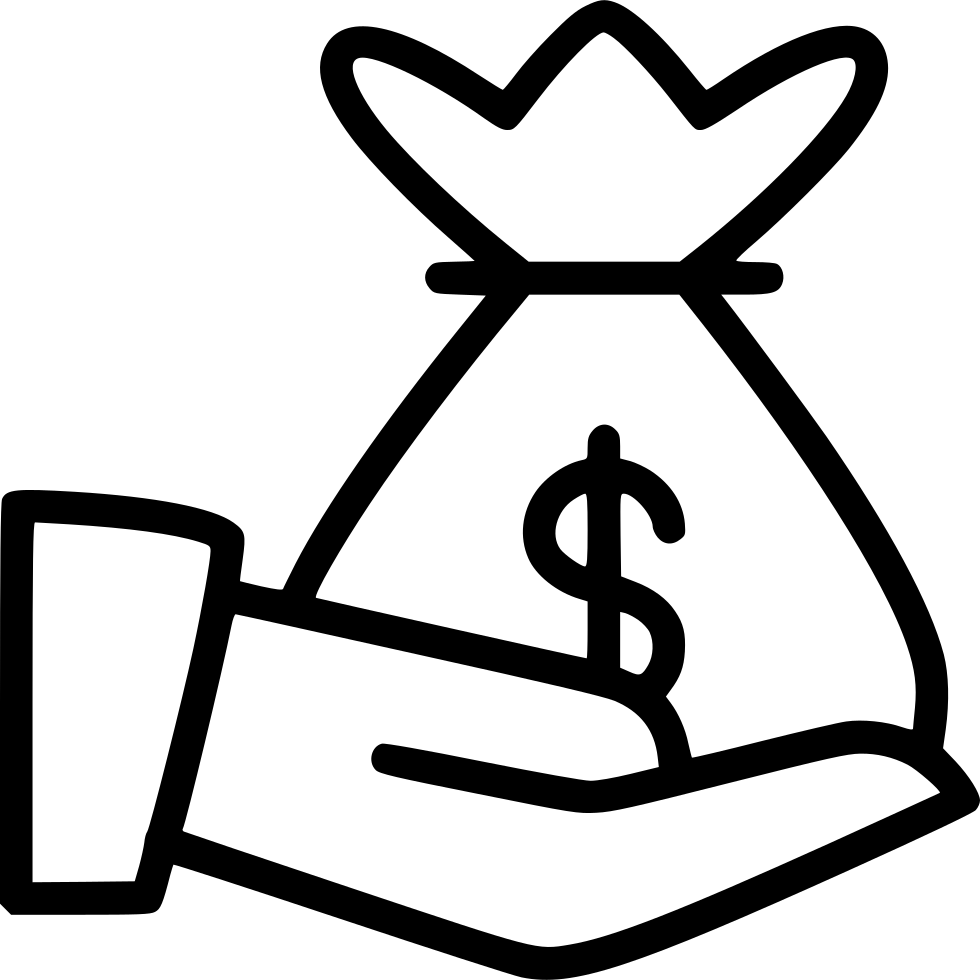
FEASIBILITY STUDY
The feasibility of the proposed AI education program was further assessed through consultation with AI experts, employee surveys, and pilot testing.
Theoretical Framework and Initial Planning
.png)
GAP ANALYSIS
Gaps in current training programs were identified, focusing on areas where AI education could add the most value, such as data analysis, machine learning, and automation.
DESIGNING THE AI EDUCATION PROGRAM
Program Specification
A detailed curriculum was developed, outlining the specific AI topics to be covered, learning objectives, and the desired skillsets for employees.
Integration Strategy
A strategy was devised for integrating AI education seamlessly into existing workflows, emphasizing real-world applications and problem-solving scenarios.
Initial Design
The program design incorporated a mix of online modules, interactive workshops, expert-led seminars, and project-based learning to cater to different learning styles.
SUPERVISED LEARNING STAGE
Content Curation
High-quality educational materials were curated, including case studies, tutorials, and industry examples, to provide a comprehensive learning experience.
Mentorship
A mentorship program was established, pairing employees with AI experts to provide guidance, answer questions, and foster a deeper understanding of AI concepts.
historical data to validate the model's effectiveness.
REINFORCEMENT LEARNING STAGE
Simulated Environment
A simulated manufacturing environment was created to allow employees to experiment with AI tools and techniques in a safe and controlled setting.exclamation
Policy Exploration
Employees were encouraged to explore different AI applications, such as predictive maintenance, anomaly detection, and quality control, through hands-on projects.
Reward System
A reward system was implemented to incentivize active participation, knowledge acquisition, and successful implementation of AI solutions exclamation.
EVALUATION AND CONTINUOUS IMPROVEMENT
Performance Metrics
Key performance indicators (KPIs) were established to measure the effectiveness of the program, including employee engagement, knowledge retention, skill development, and impact on operational efficiency.
Feedback Loops
Regular feedback was collected from employees and AI experts to identify areas for improvement and refine the program over time.
Continuous Learning
The program was designed to be adaptable and iterative, incorporating new AI technologies and best practices as they emerged.
The implementation of AI-powered tools and techniques led to significant improvements in product traceability, reducing errors and enhancing supply chain visibility.
Employees were able to identify and address inefficiencies within legacy systems, leading to increased productivity and cost savings.
The AI education program fostered a culture of continuous learning, equipping employees with valuable skills in data analysis, problem-solving, and critical thinking.
The application of AI solutions resulted in streamlined processes, reduced downtime, and improved overall operational efficiency.
Outcomes and Impact
Innovation Incubator